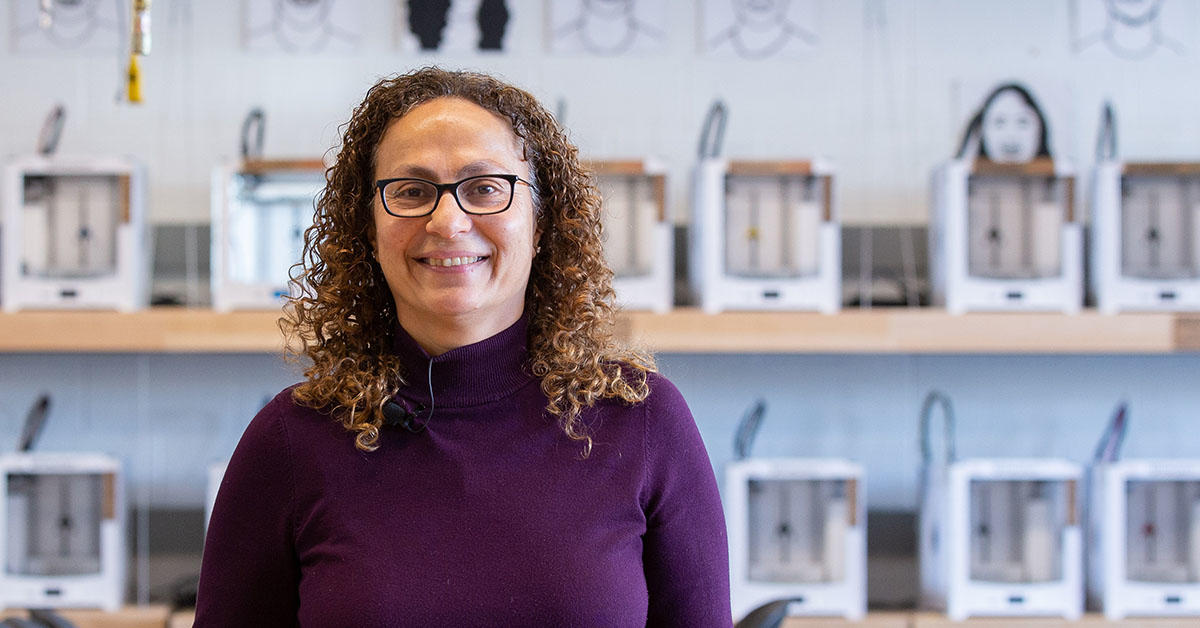
This story was updated on April 14, 2020.
Last week, the Ontario government asked manufacturers to help produce personal protective equipment for frontline healthcare workers as the threat of a shortage becomes imminent.
Engineers at the University of Ottawa were quick to answer the call. Using 3D printers and laser cutters from the Richard L’Abbé Makerspace lab on campus, a small group of students are creating plastic face shields to help fill the need.
“We all saw the horrific images coming out of Italy and I asked a few people at the Centre for Entrepreneurship and Engineering Design (CEED) to start thinking of how to help,” says Electrical Engineering Professor Hanan Anis, who heads the Makerspace lab. “Face masks were the simplest and most needed, so my student, Mohamed Elsageyer, started designing a prototype.”
The Makerspace group is producing approximately 300 masks per day. Professor Anis says that requests for masks haven’t stopped since posting about them on social media a couple of days ago.
One such request came from Dr. Bernard Leduc, President and CEO of Montfort Hospital. Through Twitter, he caught wind of what Anis and her team were developing and went to visit the Makerspace lab to get a firsthand look at the masks. He even brought some back to the hospital to use in simulations.
“The need for masks at the hospital is very urgent,” says Leduc. “We are dependent on procurement and have no idea when new masks will be delivered. If supplies don’t arrive regularly and clinical activity related to COVID-19 increases, we will face grave difficulties. In Europe, they had to resort to wearing masks for prolonged periods of time, which puts everyone at risk.”
Leduc says his colleagues at Montfort are excited to collaborate with the Makerspace team and relieved that there might be a solution to their shortage of personal protection equipment.
The group of five uOttawa engineers is continuing to make improvements to the face shields, including lengthening the mask’s visor and edges, adding padding for the forehead and strengthening the support band.
The team is also working on a prototype for a low-cost ventilator—a piece of equipment that is extremely sought after by physicians and healthcare workers in the fight against COVID-19-related fatalities.
“As engineers, we often feel helpless as we are not on the frontlines,” says Anis. “But the maker community is responding to the crisis with amazing ingenuity. This is the culture we built here, and I had no doubt that they would jump at the opportunity to help.”
The Makerspace team will also be receiving a $25,000 donation from Scotiabank, who has earmarked $2.5 million to help support community response efforts in the fight against the spread of COVID-19.
Scotiabank’s Vice-President of Global Sustainability and Social Impact, Sandra Odendahl, said the donation came together after someone on her team found an article about university engineering labs getting innovative with 3D printers to help produce protective equipment.
Odendahl reached out to professors at the University of Ottawa, where she is an alumnus of the engineering school, and other schools to see if they were working on a similar project. That’s when they learned about Anis and the face shield initiative, she says.
The students involved in this initiative are Justine Boudreau, manager of the Makerspace and Makerlab, Midia Shiekh Hassan, manager of the Makerlaunch program, and engineering students Simon Tremblay and Mohamed Elsageyer.